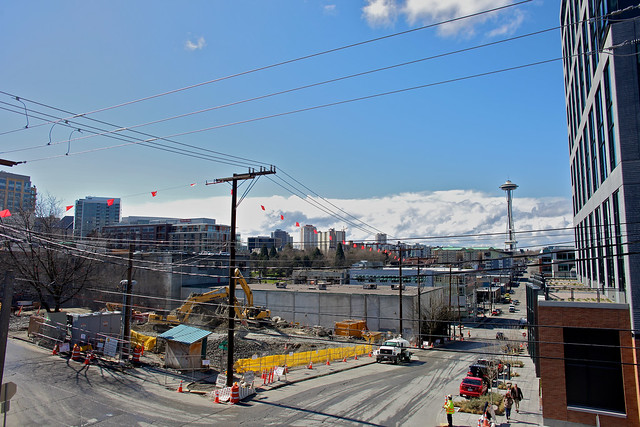
Seattle is experiencing one of, if not the greatest, building booms in its history. A short walk north from the central business district, yields sightlines filled with cranes eschewing in the beginnings of new high rise structures and large multi-family homes. Below the streets, deep and often massive trenches and excavation pits fill the ground like the great open pit mining operations of the American Southwest. Seattle’s northern skyline is stretching skyward, and it is doing so quickly.
For the average engineer and/or construction manager, this work has them anxious and excited for the present and the future. More building, means more business, and therefore more money and job security. But, for the average pedestrian waiting for the delayed 71 bus during rush hour on Fairview, 400 Fairview is a giant hole of questions, chaotic motion and a temporary distraction from yet another OneBusAway refresh update. As a construction management project engineer, I often find myself explaining to friends, family, and occasionally the random passer-by, the behind the scenes process for each of these projects. I could write ad nauseam about building a skyscraper from bottom to top, so instead I will discuss the top 5 questions I am commonly asked about large commercial and residential construction.
More after the jump.
1. How many people does it take to work a large construction project?
Projects, like Lincoln Square 2, 2210 Westlake and the Amazon Headquarters in the Denny Triangle (projects approaching and/or exceeding 1 million square feet of new construction) require countless hours of planning and careful site logistic strategies to insure the immediate surroundings can continue to operate with the smallest impact possible. Projects of this size require a project life cycle minimum of 500 working employees from numerous companies and trades around the Puget Sound region. Coordinating hundreds of people from 20-30 separate companies is a logistical nightmare. This process occurs during the bid process (if the project is a hard bid job) or during the “pre-construction” process (once a general contractor has been awarded the work). All 500 workers will not be onsite at one time, rather they will arrive and depart as the construction schedule progresses through each required trade.
2. What happens during the nights, can work occur after dark?
If it were possible/legal, general contractors would work through the night. Night hours provide the best possible time for equipment and supply delivery to site. Streets are calm and traffic mitigation is simple. Unfortunately/fortunately (depending who you are), the cities of Seattle and Bellevue have noise ordinances (6pm in Bellevue) during which no loud work can be done. This includes the operation of most if not all equipment and tools on site. Adhering to a strict 6pm work day is a practical impossibility with long concrete pours and daily rush hour traffic slowing down the most mundane tasks. The solution is city noise variances. Most of the time, a variance will be granted for certain critical path tasks, such as a large slab pour for the foundation or other issues that may arise during construction that require more than an eight to ten hour work day to complete.
3. So about the giant holes in the ground?
Large equipment arrives on site! Skyscraperpage and Skyscrapercity forum posters begin streaming photos of inactive excavators and dozers sitting motionless on an asphalt parking lot. It is a stage that screams commitment from the developer and that the bureaucratic process of permitting has given way to a soft green light of approval. Soon, thousands of truck yards of soil will be removed at a seemingly quick pace to prepare the site for the parking garage that will sit below the building. To some it may seem like a quick process and to other development enthusiasts, a painfully slow process, but most, if not all, city excavation work rates depend on how quickly a truck can arrive on site to remove the soil. For a large project, like the projects previously mention, with decent access, contractors will strive for over a hundred trucks per day until excavation is complete. Excavation durations vary from project to project, but can last from a few weeks to a few months. From this, it is logical to deduce as truck access is limited, excavation production rates will drop. A traffic jam on I-5, construction schedule delay. Mariners game, potential construction delay. These common delays can be accounted for in schedule float.
Where does all the dirt go? A common question when watching hundreds of truck loads of dirt leaving downtown Seattle each day. Locations vary, but a common answer would be “to fill up big holes”. Mining companies that have completed the process of removing precious metals, will charge companies to dump dirt back into the pit. A brilliant business practice that nets mining companies profits during the mining and reclamation process. Depending on the quality of soil, excavation spoils will also be used as fill for suburban site development or other nearby reclamation projects. It is actually quite astonishing how many holes need to be filled in the region. Even during this current construction boom, constructions companies will rarely have an issue finding a place to dump dirt.
4. How many tower cranes can you count from Kerry or Lake Union Park?
The current hot commodity in construction. With Seattle and Bellevue booming, construction cranes are on backorder and its easy to see why. Rental prices fluctuate depending on size and general supply, but typically range between $20,000 and $30,000 per month per crane. Tower cranes are essential for mobilizing materials, removing excess dirt, removing equipment from the pit, pouring concrete and aiding in site mobility. Most large new multi story buildings, excluding townhome complexes, will take advantage of a tower crane during construction. Tower cranes must be ordered and ready for delivery once excavation bottoms out. Once the desired lowest level is obtained, contractors will be quick to immediately begin pouring tower crane footings so the construction schedule can keep pace.
In areas of “tower crane congestion”, specifically South Lake Union, communication is imperative. The graphic below shows four projects in the Westlake and 9th corridor. As shown, there are 5 overlapping tower cranes in the project area. All crane operators have radio contact with adjacent operators, in addition to radio contact with their riggers on the ground. Warning systems are in place to insure adequate warning when two booms are entering shared space.
When placing a tower crane, contractors will do their best to locate the foundation outside of the building footprint. This allows for a smooth and easy demobilization of the crane when the shell of the building is complete and a tower crane is no longer required. For projects with limited space, cranes are placed in building shafts, but not elevator shafts. Once an elevator shaft is complete, contractors will begin using the elevator immediately for moving material and people, and the last thing they want in a newly completed elevator shaft, is a tower crane. A working elevator is a projects best friend.
5. How does Seattle weather play a role in building construction?
Wind, rain, and freezing temperatures constantly affect a standard construction schedule. Tower cranes can not operate when gusts of wind reach or exceed 45 mph. It is possible to shut down a tower crane if the wind is lower than 45 mph, especially when winds are swirling around the job site. Swirling wind patterns are typical for the man made canyons of an urban environment.
Rain causes excavation concerns when soil stability is compromised due to ponding in the bottom of the pit or over saturation. One inch of rain, in and open pits the size of Amazon’s new headquarters in the Denny Triangle, can produce tens of thousands of gallons of water. All of this water must be filtered and purified to an acceptable city level before water can be pumped from the pit and into the storm drainage system.
Freezing temperatures, although infrequent in the Puget Sound, must be accounted for during concrete pour days. Proper heating and tarping must be onsite to insure the concrete bonds correctly to rebar, sets up properly, and cures adequately for inspection. Freezing temperatures are easily mitigated through onsite heaters and thermal tarps to trap the heat above the curing concrete.
These five questions are just the most common questions I have heard while working in the construction management industry. Although brief, most of these answers can be expanded upon to easily fill pages and pages of books.
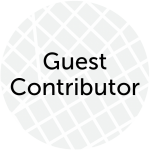